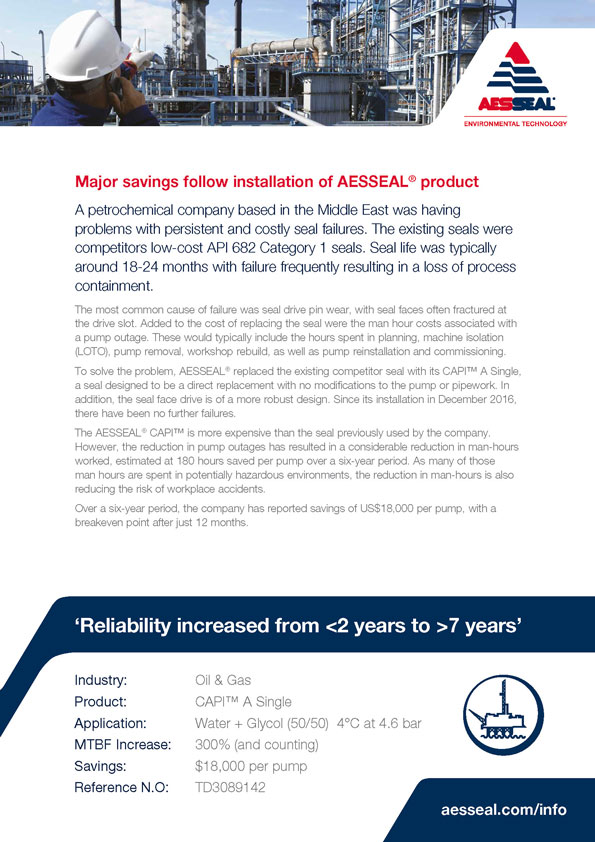
A petrochemical company based in the Middle East was having problems with persistent and costly seal failures. The existing seals were competitors low-cost API 682 Category 1 seals. Seal life was typically around 18-24 months with failure frequently resulting in a loss of process containment.
More Industry Related Content
With Richard Smith
How many pumps were affected?
The customer has a group of approximately 40 pumps which were fitted with identical competitor’s API Category 1 seals. The seals were not reliable, and would typically fail within about 18 months. The failure was normally the result of seal face fracturing. Cracks would propagate where the seal face was in contact with metal anti-rotation components. This is a common problem with this particular model / brand of seal.
What is the importance of process containment?
With hazardous materials it is important that these are contained within the equipment in order to isolate the spread of hazardous fluids (or materials) and prevent their escape to the atmosphere during the manufacturing process. The integrity and reliability of the seal prevents harm to personnel or damage to the environment, or in the case of flammable fluid, the risk of fire or explosion. The quality of the mechanical seal is vital to keeping the process fluid inside the pump casing. Failure of the seal risks loss of process containment.
Why did the company choose the CAPI A seal? What made it the best solution for this application?
We were able to demonstrate to the customer that the reliability problem could be addressed by fitting seals of a more robust design using heavier duty components. The new seals have now been fitted to all 40 pumps – all the original competitor’s seals have been swapped out in favour of the CAPI A.
Was there any pushback over the price difference? If so, how did you convince them to go with the more expensive AESSEAL product?
In fact the price difference was minimal, particularly taking into account the consequential cost of a pump seal failure, quite apart from the fact that any loss of containment involving hazardous materials represents a serious risk to personnel.
Were there any challenges or obstacles during the installation process?
We designed the CAPI seals to match up with the existing pipework. Replacing the original seals was therefore a very straightforward process. The customer was delighted with how quickly and easily we were able to change out the seals, and with the subsequent major improvement in reliability, which has resulted in major savings in labour and maintenance costs, as well as in the cost of spare parts. This greater reliability has also meant a much higher level of safety, reducing any possible risk to personnel resulting from seal failure. The seals have now been operating effectively for more than six years, compared with the previous MTBF of less than 18 months. Our level of reliability and our standard of customer service has meant that the company is now using AES products across a range of applications.