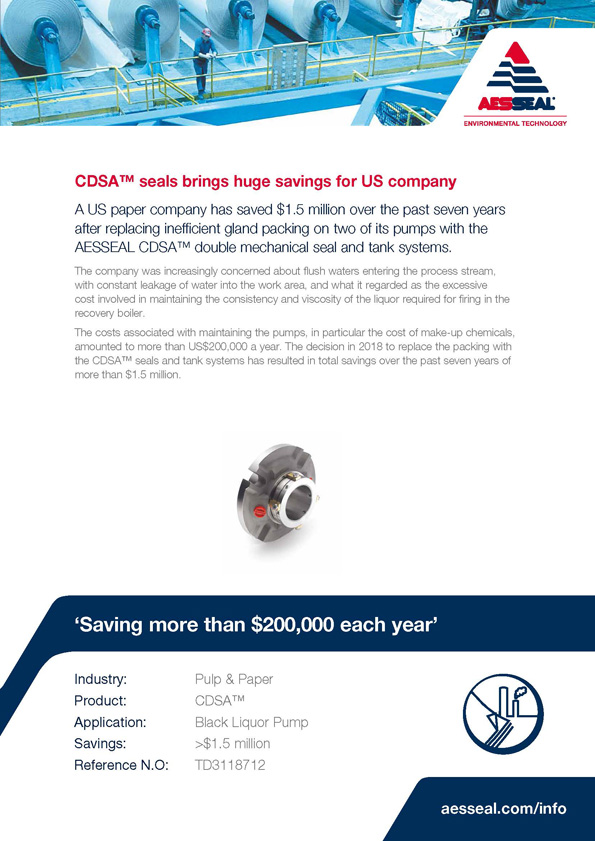
A US paper company has saved $1.5 million over the past seven years after replacing inefficient gland packing on two of its pumps with the AESSEAL CDSA™ double mechanical seal and tank systems.
More Industry Related Content
With Mike Spencer
What was the main problem the company was facing?
The main problem was with the cost of maintaining the pumps, and in particular the cost of make-up chemicals. The pumps were used to feed the recovery boiler, and the total cost of keeping them going was more than US$200,000 a year.
What was making it so expensive?
Mainly it was the cost involved in maintaining the consistency and the viscosity of the black liquor used to fire in the recovery boiler. Black liquor is a byproduct of the paper-making process. It’s used primarily in pulp and paper mills for generating electricity and for drying pulp. The company was also coping with the problem of flush water entering the process stream as well as the leakage of water into the work area.
How did the contract come about?
I made the first approach to suggest replacing the packing with the CDSA seal and tank system. The aim initially was for greater reliability and to reduce the dilution to the process stream. A further benefit has been that there is not so much need for make-up chemicals, which are added to adjust the quality of the black liquor and to aid firing in the recovery boiler.
How many pumps does the company have at this site, and how many have now been fitted with CDSA seals?
They have 250 pumps, of which they’ve converted more than 20 to CDSA™ with quotes submitted for the conversion of another 13.
What has been the feedback from the company?
They’re very pleased. The seals have performed even better than they had expected, so as a result they’re now planning to convert more of their pumps to CDSA. They estimate that they’ve saved well over a million dollars over the past seven years as a result of the decision to change to AESSEAL products. The success of this contract has also boosted our reputation with other companies in the region.