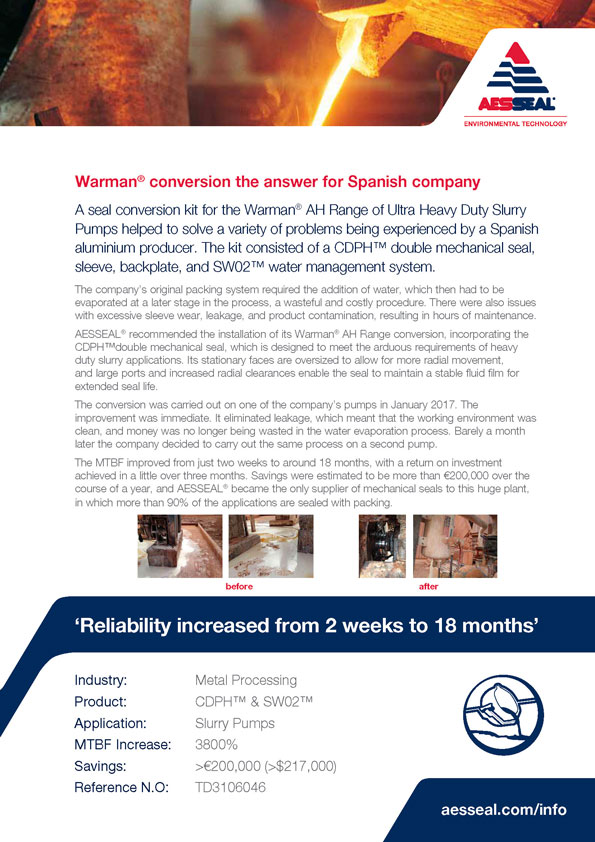
A seal conversion kit for the Warman® AH Range of Ultra Heavy Duty Slurry Pumps helped to solve a variety of problems being experienced by a Spanish aluminium producer.
More Industry Related Content
With Sergio de Gracia
What was the problem with the packing system being used by the company?
The company was using the packing as a sealing system on Warman® Ultra Heavy Duty Slurry Pumps. The problem was that it was not an efficient solution. In the first place it required water to be added to the process. The water had to be evaporated at a later stage, which meant additional cost and more maintenance. At first glance it might have looked like the cheaper option, but in fact it ends up being more expensive due to the cost of the evaporation process, the extra maintenance, and the need for certain components to be frequently replaced.
Were you aware of the problems they were having?
Yes. They were already buying our mechanical seals, and I knew that they were having problems with this packing system they were using on these heavy pumps. When I spoke to one of the maintenance staff, he agreed that it would make sense to upgrade the pumps with the conversion kit, which includes a CDPHTM double mechanical seal, sleeve, backplate, and SW02 water management system.
What convinced them that the AESSEAL system was the right solution?
They knew that we had a lot of experience working with these heavy slurry pumps, and that we were supplying all the necessary elements for the upgrade. A big factor was that there was no need for any modifications to the pumps, which made a huge difference in terms of cost.
Did the upgrade solve the problem?
Yes. Upgrading to a double mechanical seal and seal support system has resulted in better performance and lower water consumption, and it also removes the need to evaporate the water that was being added to the process when they used the packing system. It’s been estimated that in the first year alone the greater efficiency of the system saved the company around €200,000.
Why was this system a better option for this application?
Because the AESSEAL system uses clean water to cool the seal faces while also reducing the water consumption to around 20-30 litres a year, compared with the previous water consumption of eight litres a minute. It is also totally autonomous and above all, it is self-filling because it pressurizes itself with the customer's own water supply.
Were there any problems with the new system, for example during the installation process?
No, it was really easy. I was able to assist them with the installation, and it was a very straightforward procedure - essentially plug and play.
Has it operated as expected?
with it before ordering the kit for a second pump. In fact they were so impressed that they placed the second order just a month later. We are now looking at further upgrades. It’s a big plant, and most of the pumps use the old packing system, so the possibilities are there. They are also impressed with the level of customer service. I visit the site at least once a month to review the process, monitor the equipment, and help with the training of their maintenance staff. The result is that this company is doing more business with AESSEAL, and is now one of my top five customers, with lots of potential for further sales.