An Introduction To The Standard
API Standard 682 "Pumps - Shaft Sealing Systems for Centrifugal and Rotary Pumps" is the leading established industrial standard providing requirements and recommendations for mechanical seals (end-face mechanical seals) and sealing systems for use in centrifugal and rotary pumps used in the petroleum, natural gas, and chemical industries.
Published by the American Petroleum Institute (API), with the latest being the fourth edition released in 2012, the standard defines a common approach to mechanical seal design, testing, selection, as well as auxiliary seal system arrangements and piping plans.
The standard also provides a classification system for seal configurations by dividing these into common categories, types, arrangements, and orientations to ease MOC (Management of Change) processes for end user enacting like-for-like seal replacements across different seal manufacturers.
API Standard 682 is referenced normatively in API Standard 610, itself being the globally adopted standard specifying requirements for overhung, between-bearings and vertically-suspended centrifugal pumps used in the petroleum, petrochemical, and gas industries. Whilst primarily intended to define seal requirements for API Standard 610 designed pumps, API Standard 682 is applicable to both new and retrofitted pumps and to pumps designed to other standards (e.g. ASME B73.1, ASME B73.2, and API 676 pumps).
Having become such a globally renowned standard in the mechanical sealing industry, various recommendations and methodologies put forth by API Standard 682 have been adopted and good practise in non-API process industries with regard to the application of mechanical seals and sealing systems.
Please refer to our API 682 and related industry downloads and resources for further information.
API 682 Seal Qualification Testing
In order to provide end users with a high degree of confidence in mechanical seals designed in accordance with the standard, API Standard 682 requires that manufacturers conduct 'Seal Qualification Testing' (SQT) prior to market availability to a defined set of criteria, and sets minimum performance requirements for various seal configurations and arrangements.
Establishing common performance capabilities for manufacturers; Seal Qualification Tests are intended to ensure the base seal designs are adequately rated to the performance envelope defined by API Standard 682. The intent is not to perform the SQT for every individual seal cartridge or seal size in every qualification test fluid but to qualify seal configurations and attributes in specific qualification test fluids to simulate various process fluids and typical plant operation.
Whilst manufacturers are not required to run seals in all defined test media and fluids, at AESSEAL we believe to have accumulated the most appropriately comprehensive Seal Qualification Testing portfolio in the most arduous of testing regimes defined in the standard, covering flashing and non-flashing hydrocarbon duties, across the various seal arrangements and configurations in our seal range.
In essence, any API compliant mechanical seal supplied by AESSEAL is a 'clone' reproduction of those successfully subjected to the Seal Qualification Test regimes and uses the very same API 682 Qualified seal face technology.
To provide the highest level of confidence to end users AESSEAL have made available the Seal Qualification Test certificates and records for the mechanical seal product ranges below.
CAPI Seal Range
The AESSEAL API Type A, B and C mechanical seals offer the user an unprecedented range of single and dual API engineered sealing solutions to suit all application requirements. The category 1, 2 and 3 seals are qualification tested to API 682. Modular design allows the users to select the right solution for their application, with the modular design ensuring simplicity of purchase and fast delivery.
CAPI-TXS Seal Range for Non-API 610 Pump Seal Chamber Designs
The CAPI-TXS range also uses the Category 2 and 3 Seal Qualification Tested core seal components from the main CAPI seal range in adapted hardware to suit non-API 610 seal chambers. These feature typically smaller cross-sections and normally suit the lower rated Category 1 seal types. CAPI-TXS seals are available in both API 682 Type A and Type C seal arrangements. Customer specific Engineered Specials (ES) can also be supplied with these seal faces.
SMSS & DMSF Seal Range
Due to AESSEAL's unique product approach of utilising a modular product range, our SMSS and DMSF process seals utilise the same face technology as the CAPI Type A pusher seal product range. Therefore the core seal components have undergone the same API 682 qualification testing regime. As such this enables the AESSEAL to supply engineered seals that fall under the definition of 'Category 1' per API 682 but with the core seal components that have been Qualification Tested to that of Category 2 and 3 performance requirements. These seals can be suited for non-API 610 seal chamber designs, suiting smaller cross sections and bore housing but offering the full API 682 Category 2 and 3 performance envelope.
ES Seals CFC/CFFC/HPVS/HPVD
These seals are typically high duty with operating performance envelopes that exceed the definition of API 682, and as such are defined as 'ES' (Engineered Solutions). In such high duty conditions higher levels of leakage than the API 682 criteria are expected to enable performance. Whilst not subject to the same performance criteria, AESSEAL have undertaken the same Seal Qualification Test regime on to this seal technology in order to provide confidence to our customers and demonstrate they have been developed with the same rigorous amount of testing of the core seal components required by API 682 and beyond. AESSEAL have also developed face options for these seals which deliver within the API 682 performance criteria, when hardware requirements demand the ES seal solution.
API 682 Air Test
API Standard 682 requires each new or repaired mechanical seal be tested with pressurised air after final assembly. This 'Assembly Integrity Test' acts as a final acceptance test to ensure any commercially produced mechanical seal is assembled correctly and functional.
Whist not expected to be leak free, AESSEAL proved that when conducting the air test to the requirements of the standard a mechanical seal assembly is capable of successfully passing the air test performance criteria even when containing a hole as large as 0.008” (0.2mm) and is capable of leaking 270 to 1300 times that of the maximum average liquid leakage rate of 5.6 g/h API Standard 682 itself permits.
Most would agree this far from desirable for an environmental and reliability product like our mechanical seals.
As such, AESSEAL chose to go above and beyond the standard to provide the highest level of confidence in this testing for our customers, by applying a far stricter and more effective air test than required by API Standard 682.
Not only does AESSEAL apply this air testing methodology to those seal defined as 'API mechanical seals', but also to each and every process mechanical seal (non-API seals) we manufacture as standard.
For further information please refer to our posts and articles covering in detail the analysis of the API 682 air test.
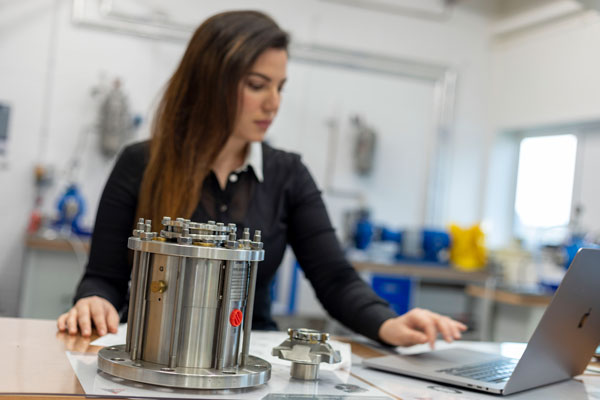
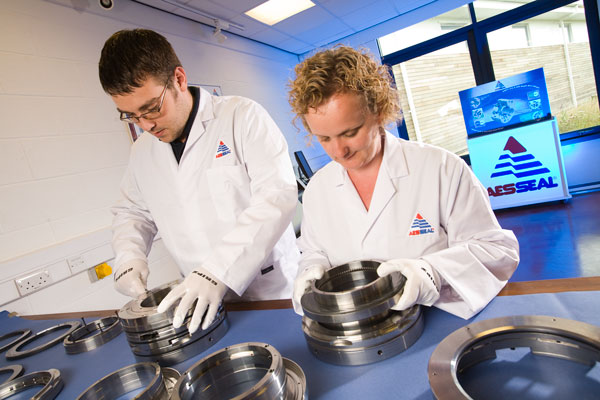
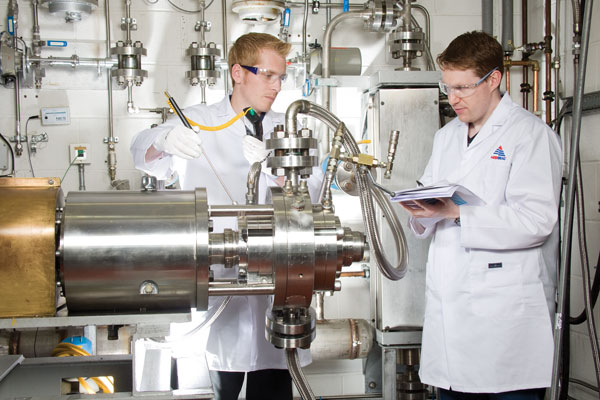
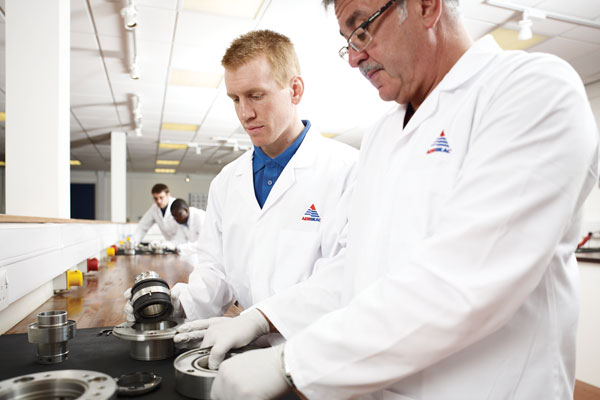